SNEC 2021: N-type technology dominates the show in Shanghai
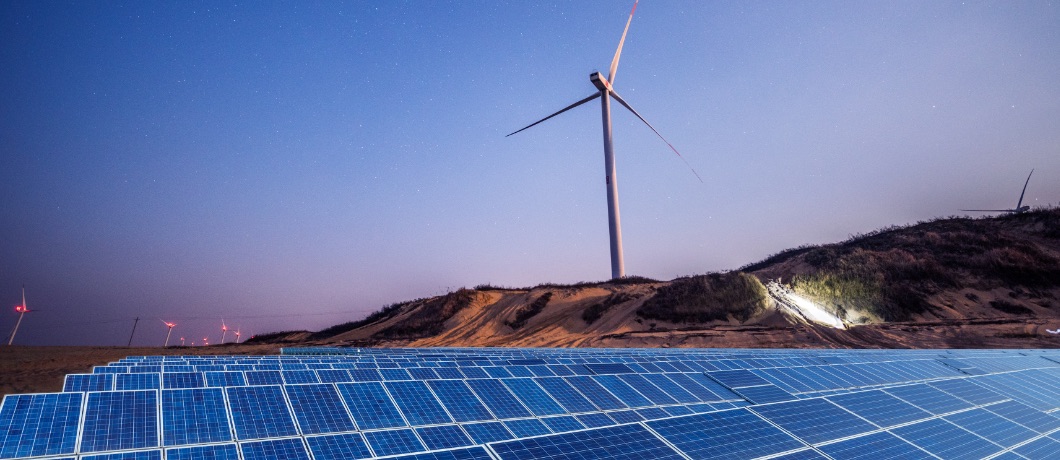
The SNEC 2021 exhibition in Shanghai was as exciting as ever and full of manufacturers showcasing their latest products and reflecting the current market developments. It was observed that module power ratings have continued to rise from last year’s 500W+ standard, with 600W+ now almost the industry standard and 700W+ the new target. One factor contributing to this increase in module power is the use of different technologies: half- or triple-cut cells, multi-busbar are becoming standardized, while n-type technologies such as TOPCon and heterojunction (HJT) are gaining an extraordinary strength and momentum.
The ever-increasing module size is also a contributing factor. As seen at the exhibition this year, 182-mm and 210-mm wafers have become mainstream, and the number of cells has also increased from 60 to 72 or even 78. For obvious reasons, the combined crystal growth and wafer station is where the shift to manufacturing larger wafers originated. As the development of wafer sizes is very fast, there will be multiple wafer sizes. However, the major sizes in the market today are M6, M10 and G12, with the majority of the industry betting that the latter two will soon dominate the market. There is no clear answer to the question of which of the two is the better choice. While M10/182mm is the wafer of choice by vertically integrated manufacturers, those not tied to wafers generally jump straight to G12/210mm. Each of these systems brings its own benefits and concerns. With wafer manufacturers from both groups expanding considerably, there are no supply-side issues from the manufacturers’ perspective. The n-type wafers in larger sizes have also begun to enter the market. The cell level is where the biggest impact is felt when it comes to wafer size change. But equipment manufacturers have done a commendable job of making this transition seamless.
Most production tools today are capable of handling all three common wafer sizes. Aside from flexibility, tool manufacturers have also adapted their equipment platforms to improve productivity in parallel. Production capacity per processing tool has improved so much that gigawatt-scale PERC fabs require only a few tools in a few processing stations. Because TOPCon processing closely follows PERC in manufacturing, tools for processing larger wafers are also available for TOPCon, while tools for HJT are in the works.
Upstream processes are not as affected by a move to larger wafers. However, because the final product has larger dimensions and is also heavier, field reliability aspects such as mechanical stress and wind resistance are areas of concern. In addition to using larger wafers, module manufacturers are also incorporating various advanced technologies – such as half-cells, MBB (multi-busbar), bifacial and narrow gap or no gap, higher CTM (cell-to-module) ratio – into these very high-power modules. The downsizing of larger wafers, usually produced in 2 or 3 pieces, to build smaller modules, is another important trend in this area.
Sourcing suitable glass for these larger modules has been a major problem for manufacturers in the past, which seems to have been solved with the huge new capacity coming on line this year. As for module width, container load capacity was the deciding factor for M10 supporters. While the size of G12 was initially believed to be an obstacle, this has been largely overcome by a different packing orientation – achieving a high packing density in kWp metric.
The larger wafer-based modules themselves come in a variety of configurations with different cell counts – 78, 72, 66, 60, 54, and even 40. These cells are usually cut into 2 pieces, but in a few cases into 3 pieces, to extract the desired electrical parameters and match them to the application. The most powerful solar module at SNEC was a TOPCon module with an output of 700 W, which also means that the concept of larger cells has gained acceptance in high-efficiency cell technology. The first large wafer-based HJT products were also on display at SNEC, the world’s largest solar exhibition held in Shanghai in June 2021.
In summary, SNEC presented the new generation of Very High-Power Modules 2021, which summarizes the key developments along the PV manufacturing and value chain that are making this approach mainstream.